Slash Your Waste, Not Your Profits: The Sustainable Superiority of the Steel Belt Conveyor
In today's fiercely competitive industrial landscape, the pursuit of efficiency is relentless. Production managers, engineers, and executives are constantly seeking ways to optimize output, reduce operational costs, and minimize downtime.
Jul 28,2025
In today's fiercely competitive industrial landscape, the pursuit of efficiency is relentless. Production managers, engineers, and executives are constantly seeking ways to optimize output, reduce operational costs, and minimize downtime. Yet, a new, equally powerful imperative has joined this pursuit: sustainability. Modern businesses are no longer judged solely on their financial performance but also on their environmental stewardship and commitment to a circular economy. The pressure is on to build greener supply chains and reduce industrial waste.Often overlooked in this high-level strategic thinking is a fundamental component of nearly every production line: the conveyor belt system. This workhorse of manufacturing, processing, and logistics can be either a significant contributor to waste and inefficiency or a powerful asset for sustainability and long-term profitability. The choice between traditional plastic or rubber belts and a modern steel belt conveyor represents a critical decision point. While the former may seem economical upfront, a deeper analysis reveals a hidden story of frequent replacements, high maintenance, energy waste, and significant environmental burden. This article will dissect this comparison, exploring why durability is the ultimate key to cutting waste and how the intrinsic properties of steel create a cascade of benefits for your operations, your budget, and the planet.
Table of contents:
A Deep Dive into the Material Showdown
The Ripple Effect on Environmental Sustainability
Boosting Efficiency in Energy and Operations
The Financial & Reputational Bottom Line
A Deep Dive into the Material Showdown
The core difference between these two systems begins at the molecular level. The material you choose for your conveyer belt dictates its performance across every critical metric, from its lifespan to its suitability for specialized applications.
1. The Chasm in Lifespan and Replacement Frequency
The most direct way a conveyor contributes to waste is through its own disposal. Here, the contrast is stark. Plastic and rubber belts are susceptible to the cumulative effects of mechanical stress, temperature fluctuations, and chemical exposure. They stretch, fray, tear, and degrade. In many demanding industrial environments, their operational lifespan is measured in months, often requiring replacement every 1 to 3 years. Each replacement cycle generates significant landfill waste and incurs costs for the new belt, labor, and lost production time.
In contrast, a steel belt is engineered for longevity. Made from durable stainless or carbon steel, its average lifespan can easily exceed a decade, with many systems operating flawlessly for 20 years or more. This exceptional durability means a single steel belt can outlast ten or more plastic belts. This drastically reduces the primary source of conveyor-related waste—the belt itself—and transforms a recurring operational expense into a long-term capital investment.
2. Unmatched Resilience to Thermal and Chemical Extremes
Many production processes involve extreme conditions that are simply hostile to polymers. Consider a bakery oven, a flash-freezing tunnel, or a chemical processing line. A plastic or rubber conveyer belt in these environments will quickly show signs of distress. High temperatures can cause them to soften, melt, or release harmful fumes. Extreme cold can make them brittle and prone to cracking. Corrosive chemicals can eat away at the material, compromising its structural integrity and potentially contaminating the product.
This is where a Steel belt conveyor demonstrates its inherent superiority. Steel is exceptionally resistant to both high and low temperatures, maintaining its flat, stable surface from -80°C to +400°C (-112°F to +750°F) and beyond in some applications. It is also impervious to most oils, fats, and corrosive chemicals. This resilience ensures consistent, reliable performance in the toughest conditions, eliminating the risk of belt failure and product contamination that plagues its plastic counterparts.
3. Setting the Gold Standard for Hygiene and Safety
In the food, pharmaceutical, and electronics industries, hygiene is not a preference; it is a strict regulatory requirement. Plastic and rubber belts, being porous materials, are prone to microscopic cracks and scratches over time. These imperfections become breeding grounds for bacteria and allergens, making effective sanitization difficult and creating a constant risk of cross-contamination. The material can also absorb oils and residues, leading to odors and product spoilage.
A solid steel belt presents a smooth, non-porous, and crack-free surface. There are no crevices for bacteria to hide. This makes it incredibly easy to clean and sanitize, meeting the world’s most stringent hygiene standards like those from the FDA and EU. Residues can be scraped off or washed away completely, ensuring a sterile processing environment. This makes steel the undisputed material of choice for applications where product purity and consumer safety are paramount.
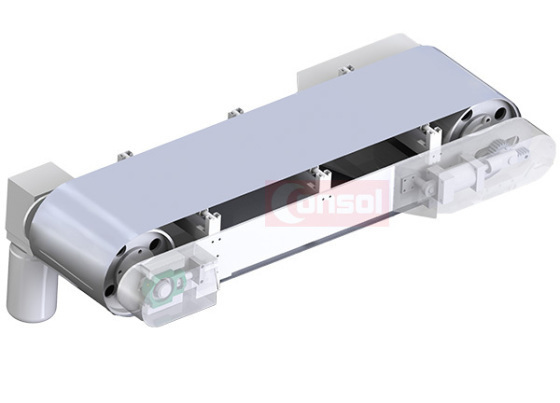
The Ripple Effect on Environmental Sustainability
A durable product is inherently a sustainable one. The benefits of a steel belt extend far beyond its own long life, creating a positive environmental impact throughout the operational lifecycle.
4. The Circular Economy Advantage: True Recyclability
Sustainability in the 21st century is defined by the principles of the circular economy: reduce, reuse, and recycle. When a plastic conveyor belt reaches the end of its short life, its destination is almost always a landfill. Even if recycling is attempted, plastics are typically downcycled into lower-grade products, and the process itself is energy-intensive.
Steel, however, is one of the world's most recycled materials. At the end of its multi-decade service life, a steel conveyor belt can be melted down and repurposed into new, high-quality steel products with no degradation in quality. It is 100% recyclable. Choosing a Steel belt conveyor means you are not just buying a durable piece of equipment; you are investing in a material that can be infinitely reborn, completely closing the loop and eliminating landfill waste.
5. Minimizing Secondary Waste from Maintenance
The environmental impact of a conveyor belt system isn't limited to the belt itself. Frequent maintenance and repairs on plastic belts generate a stream of secondary waste. This includes discarded spare parts like rollers and bearings worn down by high friction, used lubricants, and chemical-laden cleaning agents required for deep sanitation. The carbon footprint of manufacturing and shipping these replacement parts multiple times a year adds up significantly.
Because steel belts require far less maintenance and have fewer wearing parts, this entire ecosystem of secondary waste is drastically reduced. Their robust nature means fewer emergency repairs, less consumption of spare parts, and a lower overall resource drain on your maintenance department and the environment.
Boosting Efficiency in Energy and Operations
A sustainable solution must also be an economically sound one, driven by operational excellence. Here again, the physical properties of steel provide a distinct advantage.
6. The Physics of Efficiency: Lower Friction, Lower Energy
A key hidden cost of any conveyor system is energy consumption. Plastic and rubber belts have a relatively high coefficient of friction, meaning they require more energy to pull along the conveyor frame. They also have a tendency to stretch and slip, demanding constant tensioning and leading to wasted motor power.
The flat, smooth surface of a steel belt glides with minimal friction. This translates directly into lower energy requirements to drive the system. When paired with modern variable frequency drives (VFDs) that adjust motor speed to the precise demand, the energy savings can be substantial—often reducing electricity consumption by 15% or more compared to a comparable plastic belt system. Over a decade of operation, these savings represent a significant return on investment.
7. The High Cost of Downtime: Maximizing Uptime and Productivity
For any manufacturing plant, unscheduled downtime is the enemy of profitability. Every minute the line is stopped for a belt replacement or repair means lost output, idle labor, and potential shipment delays. Given their propensity for tearing and failure, plastic belts are a common source of unexpected and costly downtime.
The reliability of a steel belt conveyor is one of its most compelling financial benefits. Its resistance to damage and wear means planned downtime is minimal and unscheduled stops are virtually eliminated. This ensures a stable, continuous production flow, allowing your facility to maximize its capacity and meet output targets consistently. This operational stability is a cornerstone of a lean and profitable manufacturing strategy.
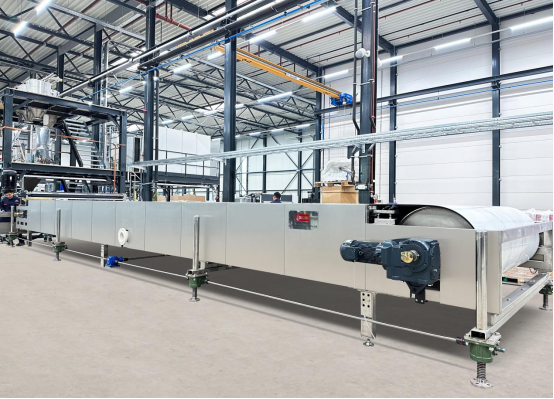
The Financial & Reputational Bottom Line
Ultimately, the decision to invest in a specific technology must be justified by its return on investment and its impact on the company’s brand.
8. Beyond the Sticker Price: A Superior Total Cost of Ownership (TCO)
It is true that the initial capital expenditure for a steel belt system is higher than for a plastic one. However, focusing solely on the upfront price is a classic business pitfall. The true financial measure is the Total Cost of Ownership (TCO) over the system's life.
When you factor in the repeated cost of replacement belts, the labor for installation, the production losses from downtime, the higher energy consumption, and the intensive maintenance required for plastic belts, the financial picture flips. Over a 5 or 10-year period, the steel belt conveyor consistently delivers a lower TCO. It is a strategic investment that pays dividends year after year.
9. Boosting Your Brand: ESG Ratings and Customer Trust
In an increasingly transparent world, a company’s environmental, social, and governance (ESG) performance is scrutinized by investors, partners, and customers. A strong ESG profile can unlock preferential financing, attract top talent, and build powerful brand loyalty.
Integrating long-lasting, recyclable steel belts into your production is a tangible and reportable action that strengthens your sustainability credentials. It demonstrates a concrete commitment to reducing waste and improving energy efficiency. This can be a powerful story to tell in sustainability reports, investor briefings, and marketing materials, helping to build trust and differentiate your brand as a responsible industry leader.
The global market is shifting as consumers demand sustainable products and corporations adopt green procurement policies. To stay competitive, especially in eco-conscious markets like the EU and North America, businesses must prioritize sustainability. Choosing a durable, efficient conveyor belt system not only optimizes operations but also positions your company as a valuable partner in green value chains. It’s a strategic advantage that showcases forward-thinking and helps attract new business.The evidence is clear: the choice of a conveyor belt is far more than a simple operational detail. It is a strategic decision that impacts everything from your bottom line to your brand reputation. By prioritizing durability, you inherently choose a path of reduced waste, lower costs, and enhanced sustainability.For businesses ready to make this strategic shift, partnering with expert conveyor belt manufacturers is essential. Companies like CONSOL specialize in engineering high-performance Steel belt conveyor solutions that are tailored to the unique demands of various industries, providing the technology and expertise to turn the promise of durability into a tangible operational and environmental victory.
Related Posts
Steel belt pastillator granulation production line for jewelry wax middle temperature wax
Rotary belt condensation pastillator granulator&pelletizer is using low melting point characteristic of the material (50 ℃ to 300 ℃), through the feeding head, the liquid material will drop into the upstream moving steel belt,with the continuous spray cooling device set at the bottom of the steel belt (spray type water cooling), materials will be cooled quickly and become solidification in the process of conveying
Contact Us
E-mail
info2@consolbelts.com
Phone/WhatsApp/Wechat
+86 18820135908